Explosion Control of Energy Storage Systems - Challenges + Opportunities
Stefan Kraft + Anil Kapahi
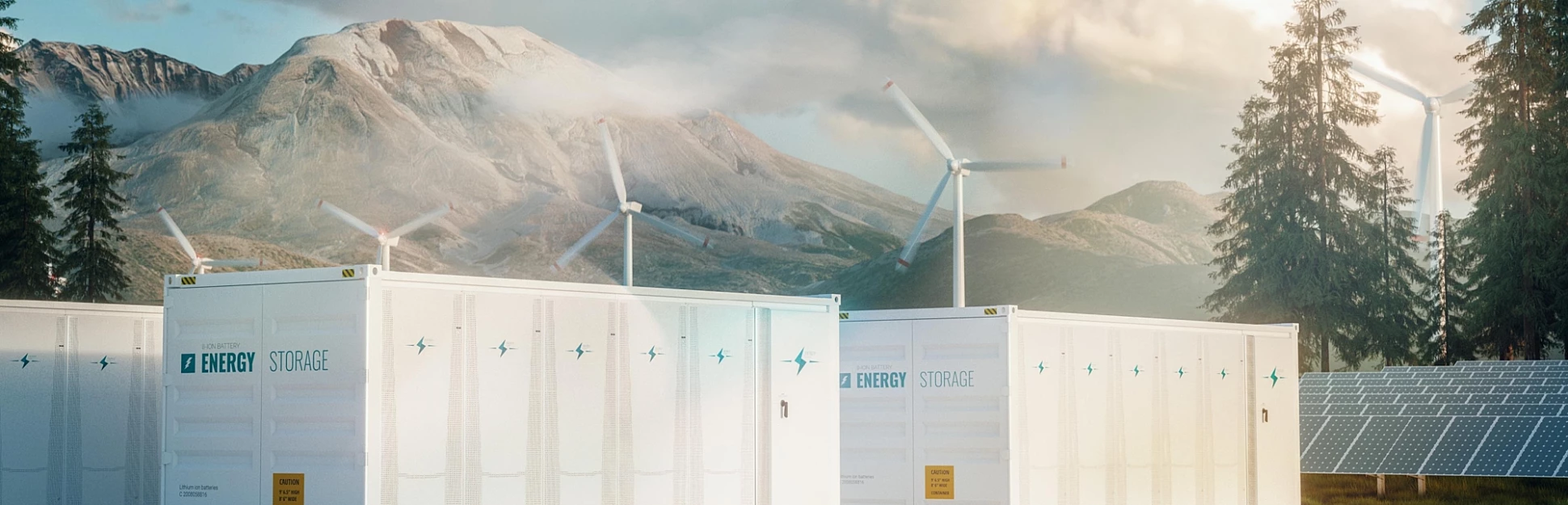
Nov 13, 2024
Introduction — ESS Explosion Hazards
Energy storage systems (ESS) are being installed in the United States and all over the world at an accelerating rate, and the majority of these installations use lithium-ion-based battery technology. For grid-scale and residential applications of ESS, explosion hazards are a significant concern due to the propensity of lithium-ion batteries to undergo thermal runaway, which causes a release of flammable gases composed of hydrogen, hydrocarbons (e.g. methane, ethylene, etc.), carbon monoxide, and carbon dioxide. The fire codes (IFC 2021 Chapter 1207, NFPA 855 ed. 2023) contain a requirement to include explosion protection for installed systems exceeding certain energy capacity thresholds. This requirement can be satisfied using passive protection methods such as deflagration venting according to NFPA 68 or active methods such as those specified in NFPA 69 (ed. 2024) that involve combustible concentration reduction using mechanical exhaust ventilation.
Both strategies have been used in the process safety industry for many years, but the design of modern ESS systems provides unique challenges with highly congested geometries in an enclosed environment and a stochastic hazard. Currently, technical gaps exist in the use of NFPA 68 and NFPA 69 for ESS containers, and thus a redundant approach is recommended to enhance safety. Although passive protection is a nearly maintenance-free solution, the prescriptive calculation methodology of a deflagration vent design according to NFPA 68 and its applicability to ESS-type designs is questionable. Active systems according to NFPA 69 such as mechanical exhaust ventilation are commonly used in the ESS industry, but their design is typically based on limited test data and an engineering analysis using assumptions for the progression of the failure event. Field incidents have different failure modes than those used in standardized battery testing such as UL 9540A, leading to ambiguous design bases. Furthermore, the need to perform routine inspections and the maintenance of backup power during a failure event reduces the reliability of active systems. The first part of this article highlights the applicability and limitations of active and passive strategies. In the second part, some specific gaps are identified in the NFPA 68 prescriptive deflagration vent area calculation methodology. A summary of available validation data is provided with a recommendation to create ESS-specific validation test data to fill existing gaps.
Current Protection Methodologies and Their Limitations
Economic factors in the energy storage industry typically lead to tightly packed ESS enclosures that cause difficulties in designing feasible explosion control solutions. Several competing design objectives for ESS can detrimentally affect fire and explosion safety, including the hot aisle/cold aisle layout for cooling efficiency, protection against water and dust ingress into the enclosure, and the use of larger cells with increased energy density. These objectives result in a highly congested enclosure with numerous obstructions, requiring only a small number of cells undergoing thermal runaway to create an explosible environment. Figure 1 shows the enclosure layout of the APS ESS installation that experienced an explosion event in 2019, which is an example of a congested enclosure using a large amount of equipment.[1]
The two types of explosion control options for ESS, NFPA 68 deflagration venting and NFPA 69 exhaust ventilation, are based on a design basis determined from UL 9540A test data. This testing is meant to provide baseline data for the analysis and is generally extrapolated to a sufficiently conservative hazard scenario for the ESS installation.
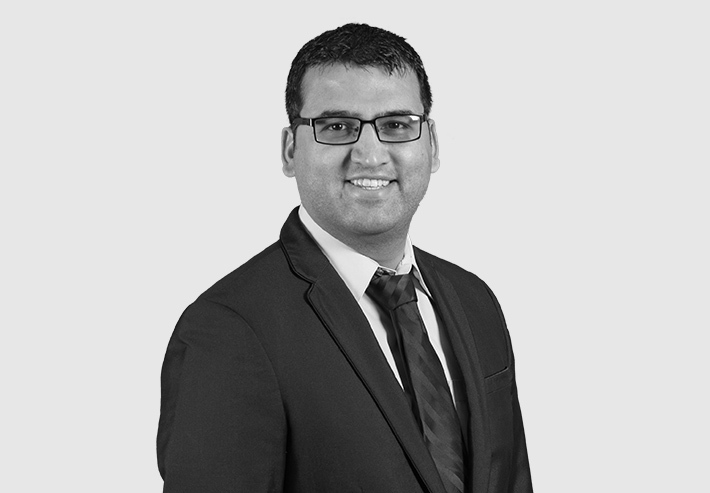
About the author
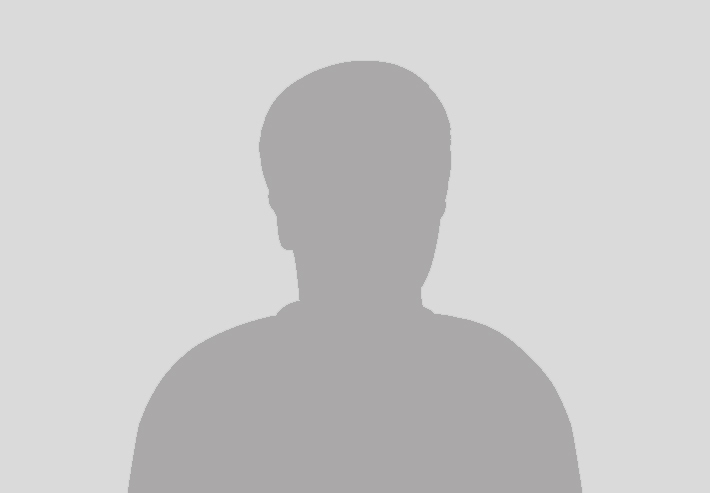
About the author