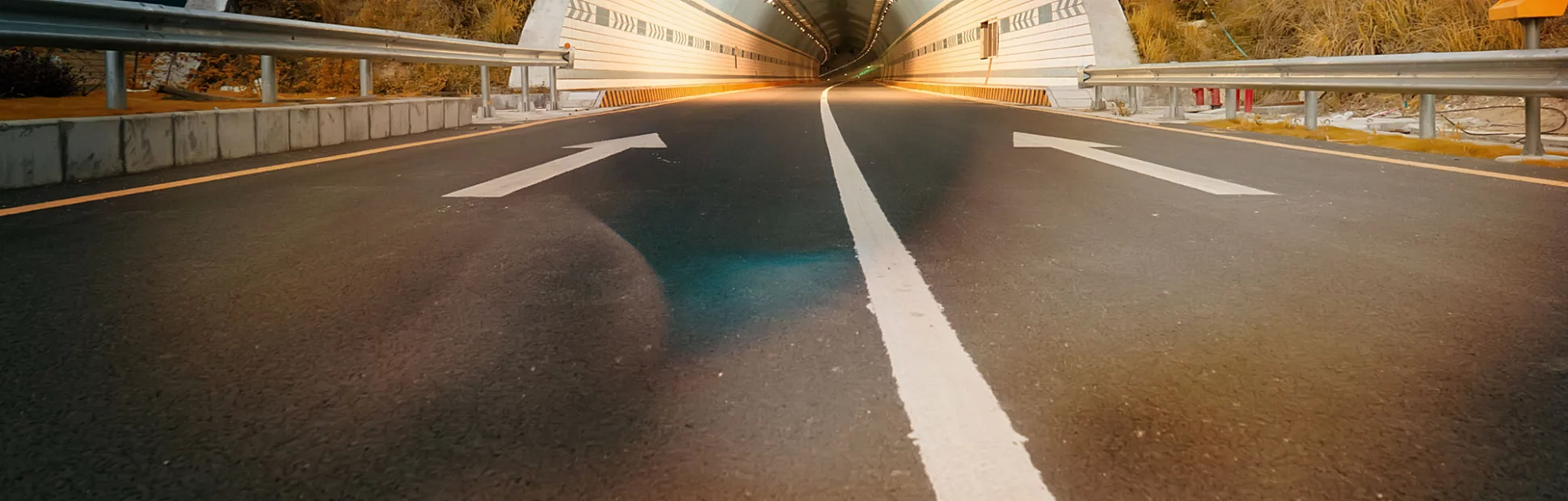
How Pavement Defects Contribute to Hydroplaning Vehicle Accidents
Hydroplaning and loss of skid resistance are well-known causes of fatal vehicle accidents. During periods of abnormally heavy rainfall, water can build up on well-constructed, properly-mixed pavements. Persons traveling at normal but significant rates of velocity (40 MPH or higher) with proper tire tread depth can experience hydroplaning or loss of skid resistance in these conditions. During periods of light rainfall, however, if a relatively new highway surface collects water (i.e., ponding) or loses its skid resistance, it is likely that a defect is present in the pavement. Understanding the types of pavement defects and placement problems that can occur with Portland Cement Concrete (PCC) and Hot Mix Asphalt (HMA) is essential to determining the potential causes of hydroplaning and loss of skid resistance in an accident investigation.
Portland Cement Concrete Pavements
To determine if a PCC pavement is acceptable, Department of Transportation (DOT) personnel and highway contractors rely on the amount of slump and percentage of air entrainment in the wet PCC mix, which are both determined on-site. They also rely on the compressive strength of the hardened concrete, usually tested at 7-, 14- and 28-day intervals after the PCC has been placed. However, these tests cannot be relied upon to determine the quality and quantity of the aggregate (rocks and sand) and other additives nor can they determine if the PCC was properly placed on-site.
PCC pavement mix defects and placement problems that can contribute to loss of skid resistance and hydroplaning include:
- Polishing Aggregates. Over time, PCC pavement surfaces containing limestone, dolomite and other soft aggregates will become polished under traffic loading and provide little or no skid resistance.
- Improper Fine Aggregate (Sand) Size and Shape. The quality of the fine aggregate is very important in PCC pavement. If the size and shape of the aggregate does not meet construction specifications, the bond between the sand and cement could be weakened causing the surface to polish.
- Improper Finishing of PCC Pavement. Once a PCC pavement is placed, it is usually machine finished before grooving or tining. Overworking the PCC pavement finish with a hand trowel, however, may cause an undesired change in the water/cement ratio at the surface. As a result, the concrete surface may spall in the wheel tracks causing loss of skid resistance or ponding of water.
- Placement of PCC Pavement in Cold Weather. While not a routine issue, there are cases where problems occurred as a result of PCC pavements being placed in cold weather (less than 40°F). These situations involved the use of high, early-strength concrete to allow for application of traffic loads within hours of placing the PCC pavement. The water temperature in a PCC mix is critical to bonding the cement to the aggregate and should be at least 50°F. If the water temperature is too low to properly bond the cement to the aggregate (approximately 33°F), water-collecting ruts can form in the wheel tracks when traffic loads are applied.
Hot Mix Asphalt Pavements
Because HMA pavements typically cost less to build and maintain, most interstate, state and county highways are constructed with HMA pavements. Although polishing of the HMA pavement can occur with the use of improper aggregate, HMA pavements are more susceptible to rutting. Rutting will occur if any one of several HMA pavement mix design variables is adversely changed or the highway contractor improperly places the HMA pavement. Because of the susceptibility of HMA pavements to rutting (and eventual hydroplaning), greater care must be taken in the design and construction process.
HMA pavement mix defects and placement problems that can contribute to skidding, rutting and hydroplaning include:
- Improper Compaction of In-Place HMA Pavements. One indicator of a properly compacted HMA pavement is the percentage of air voids in the mix. If the HMA pavement is over-compacted during initial placement, the percentage of air voids will be low causing plastic flow of the mix and rutting in the wheel tracks. If the HMA pavement is under-compacted during initial placement, the percentage of air voids will be high causing ruts to form when traffic loading compacts the mix.
- Excessive Asphalt Cement Content. Excessive asphalt cement (AC) will fill desired air voids in the HMA pavement intended to provide stability to the HMA pavement under traffic loading. The HMA pavement will become “plastic” and ruts will permanently form in the wheel tracks. Evidence of excessive AC content include rutting and large, hardened spots of bleeding asphalt cement.
- High Dust/Asphalt Weight Ratio. The normal range for this ratio is 0.6 to 1.2. When too much dust is added to the mix, the ability of the AC to bond with fine and coarse aggregates is lessened resulting in cracking and rutting.
- Polishing Aggregates. Similar to PCC pavement surfaces, HMA pavements containing limestone, dolomite and other soft aggregates will become polished under traffic loading over time and result in loss of skid resistance.
- Improper Coarse Aggregate (Rock) Size and Shape. The quality of the coarse aggregate is most important in HMA pavement. If the size and shape of the aggregate does not meet construction specifications, the bond between the rocks and AC could be weakened causing rutting to occur. In addition, rounded rocks (like river stones) provide less skid resistance than angular, multi-surface rocks.
Accident Reconstruction and Pavement Testing
Once it’s determined that skidding or hydroplaning caused an vehicle accident, it’s important to quickly establish the construction history of the incident area and if the pavement surface or composition was a contributing factor. Highway maintenance and improvements can significantly alter the pavement surface and composition. If rutting is present, the depth of the ruts must be measured. The measurement of the ruts, plus any other incident scene measurements, should be taken during an accident reconstruction investigation if the incident scene has not been significantly altered.
It is highly recommended that all pavement samples taken to test for defects be considered legal evidence. Documentation to assure a proper chain of evidence is necessary to satisfy all potential parties that the pavement samples were carefully retrieved, stored and submitted to the testing laboratory. Additionally, pavement samples should be tested with calibrated equipment, and national and/or state testing standards and procedures should be used to assure reliable and consistent test results.
Leave No Stone Unturned
Examining the vehicles, road conditions, weather, surrounding environment, and driver or passenger circumstances are all critical elements to accident reconstruction. Jensen Hughes’ forensics experts have investigated thousands of collisions as well as complex vehicle accidents involving hydroplaning and loss of skid resistance. Learn more about how we can assist with your investigation.
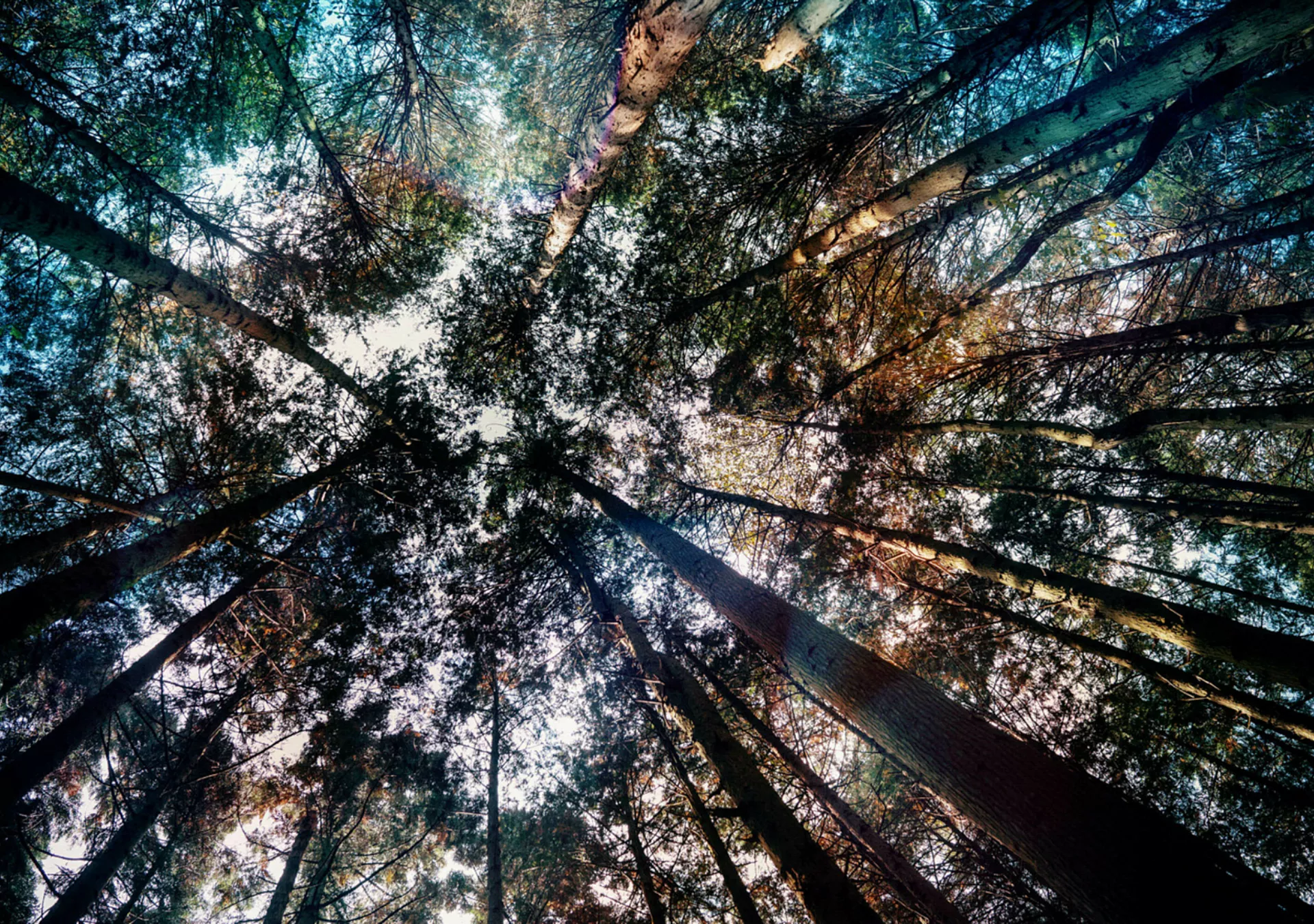