PSM and RMP "Magic Words"
Gayle Nicoll
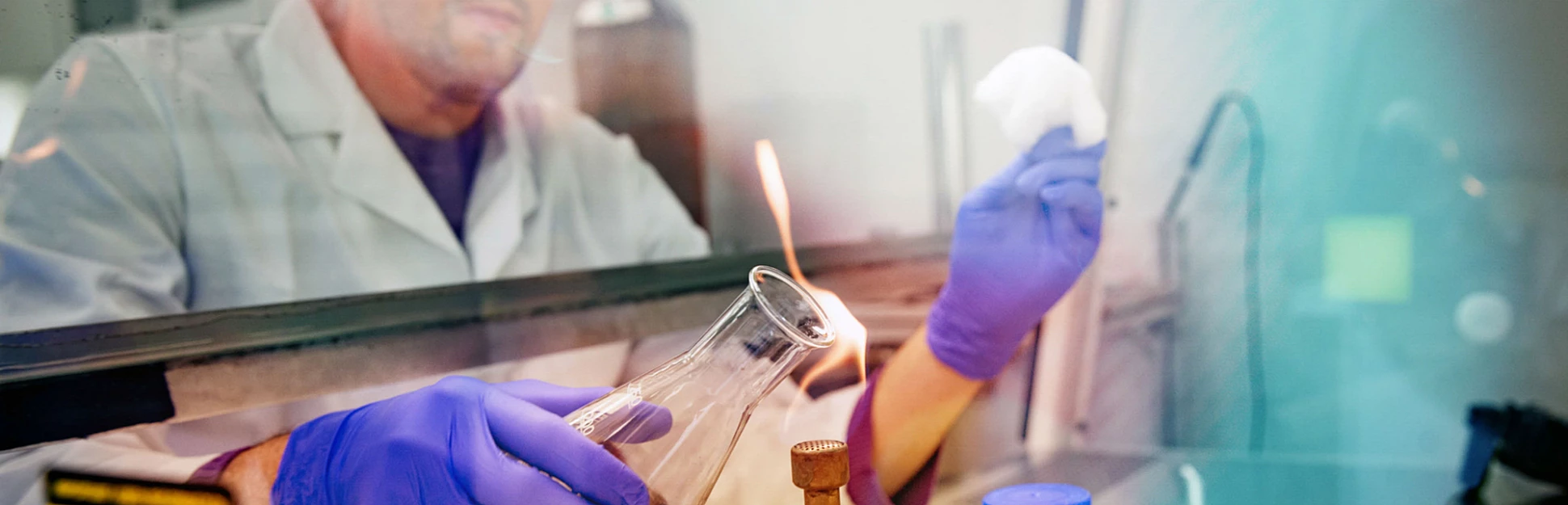
Mar 21, 2025
Summary
Complying with the Occupational Safety and Health Administration’s (OSHA) Process Safety Management (PSM) and the U.S. Environmental Protection Agency’s (EPA) Risk Management Program (RMP) regulations can seem a bit daunting. Over the years of auditing and assisting clients in developing their programs, I’ve noticed that some requirements are often overlooked or missed simply because people do not understand that the facility should include what I call “magic words” in their PSM or RMP documentation.
As an example, OSHA’s requirements for an Emergency Action Plan (EAP), found at 29 CFR 1910.38, require that the EAP include “…procedures to be followed by employees who remain to operate critical plant operations before they evacuate.” Many EAPs do not include a specific section to address this topic, and when I ask “Why?” during an audit, the facility personnel state that they do not require employees to remain behind, so they did not include this section in the EAP. While this may seem logical, from a compliance auditing standpoint, this means the facility has a potential gap in its EAP. A better tactic is to include those “magic words” and then briefly state that the facility does not require personnel to stay behind to operate plant equipment. That way, the facility has documented their familiarity with the regulation and demonstrated that they have considered the requirement.
In this white paper, we’ll discuss several process safety topics where “magic words” play a key role:
- Operating procedures
- Pre-startup safety review
- Mechanical integrity
- Management of change
- Incident investigation
- Emergency response
Operating Procedures
Operating procedures must meet several requirements, often resulting in lengthy documents. Nevertheless, these procedures must include the following “magic words” to be compliant.
- Operating phases: Both OSHA and the EPA require the following seven topics be addressed in operating procedures. Facilities may have one procedure that includes all seven operating phases, or seven different documents. The key is to make sure that each of these seven “magic words” make it into your facility’s operating procedures.
- Initial startup: If your company runs 24/7, then you may only need to use this procedure once during the commissioning of the process. Or your process may start at the beginning of each day. Regardless, you need step-by-step procedures for startup.
- Normal operations: This is by far the most common mode of operation, and the one that most facilities have available for review. However, oftentimes, the procedure doesn’t have the phrase “normal operations” in the document. Best practice is to include these “magic words.”
- Temporary operations: These “magic words” get omitted a lot, especially by facilities that do not have a temporary operation mode. If your facility does not allow the process to run temporarily, your operating procedures should still have a section called “temporary operations,” where you specifically state, “no temporary operation of this process is allowed.”
- Emergency shutdown: Best practice is to place the emergency shutdown procedures at the front of a procedure or binder so that operators can easily find them in the case of an emergency.
- Emergency operations: This is another section that frequently gets omitted from operating procedures. Many times, the facility does not allow the process to run under emergency conditions. In this case, include the header “emergency operations,” then state that the process is not allowed to run during an emergency.
- Normal shutdown: Sometimes, “normal shutdown” is the same as “emergency shutdown,” or vice-versa. As a result, the facility included one of these “magic words,” but not the other. If these shutdown methods are the same, the best practice is still to have both sections and cross-reference them or reiterate the same steps in both sections.
- Startup following a turnaround (or after emergency shutdown): This may be the same as “initial startup,” in which case, the operating procedures may not contain these “magic words.” Best practice is to include each one of these seven headers and cross-reference the other section or repeat the steps for each section as appropriate.
- Operating limits: Operating procedures need to have a section called “operating limits,” which should contain the following information or cross-reference to the appropriate Process Safety Information (PSI) that contains this information.
- Consequences of deviation: For each process parameter (i.e., flow, temperature, pressure, level), the operating procedures should outline what would happen to the process if the parameters were both too high and too low. Oftentimes, this is summarized in table format for ease of reference.
- Steps required to correct or avoid a deviation: These should be specific steps that operators can take to bring the parameter back into normal operational levels. This is also often included as part of a table. Make sure to title each column in the table with the appropriate “magic words.”
- Safety & health considerations: This is a section that is often missed in operating procedures. Facilities state that they don’t include this section because the employees are expected to refer to the applicable Safety Data Sheets (SDS) for this information. However, the SDS does not fulfill all of the requirements below. The facility should include the “magic words,” and can then direct employees within the operating procedure to the applicable SDS for further information.
- Properties of, and hazards presented by the chemicals: This is the first subset of requirements under the Safety & Health Considerations section, required by both OSHA PSM and the EPA RMP. This information may be in the SDS, and the procedure can reference the SDS.
- Precautions necessary to prevent exposure: This information is not explicitly contained in the SDS and is process- and procedure-specific. Therefore, the facility needs to list the specific precautions that the employees should take to prevent chemical exposure.
- Control measures to be taken if physical contact or airborne exposure occurs: While some of this information may be in the SDS, the information is generic and not process-specific. The facility should detail specific steps related to the process that employees can take once they have been exposed to a process chemical.
- Quality control for raw materials and control of hazardous chemical inventory levels: Many operating procedures are missing these “magic words.” Most people I talk to do not understand why this information belongs in an operating procedure, explaining that operators do not care. While this may be true, the regulation still requires that this information be addressed in the operating procedure. Note, however, that you can cross-reference to another document or resource where the information is contained.
- Special or unique hazards: Many facilities are tempted to cross-reference the SDS for this requirement, but this may not meet the intent of the regulation. The idea is to remind employees of the hazards associated with the chemicals they are interacting with in the process, which may not be apparent when reviewing the SDS. A great example of this is anhydrous ammonia. Section 2 for most anhydrous ammonia SDSs has the pictograms for Gas Under Pressure, Corrosive, Irritant, and Toxic to Aquatic Life. Some SDSs for anhydrous ammonia do not mention ammonia’s ability to interact with water vapor and recent rainfall to form a toxic cloud.
- Safety systems and their functions: The operating procedure should include these “magic words,” along with either a list of the safety systems and what each one does, or a cross-reference to another document that contains this information.
Pre-Startup Safety Review (PSSR)
The PSSR process takes many different forms and implementation strategies, which is allowed by the regulations. Regardless of what process your facility has for PSSR, the review must contain each of the following “magic words.”
- Equipment design specification review: The facility needs to document that the equipment was designed appropriately during the PSSR. This should be more than one check box that states that a review was performed.
- Operating procedure development/update/review: Even if no procedures were updated as part of the change, the PSSR should still document that personnel thought about whether operating procedures needed to be created, reviewed, and/or updated as part of the PSSR.
- Maintenance procedure development/update/review: Likewise, even if no maintenance procedures were updated as part of the change, the PSSR should still document that personnel thought about whether maintenance procedures needed to be created, reviewed, and/or updated as part of the PSSR.
- Process hazard analysis (PHA): Major changes that affect the process or create a new process may need to go through a PHA prior to startup. The evaluation of whether a PHA should be performed or not should be captured as part of the PSSR.
- Training: Even minor changes require that affected personnel be trained. One of the most common gaps I see when auditing is that the facility did not have evidence that employees had been trained on the change.
Mechanical Integrity
Ideally, your facility should have a policy document for mechanical integrity. This policy document should have the following headings, among others:
- RAGAGEPs: This is the acronym for “recognized and generally accepted good engineering practices.” RAGAGEPs include widely adopted codes, such as NFPA; consensus documents, like ASME; non-consensus documents, like the CGA pamphlets; and internal standards, such as an organization’s global engineering standards. At a minimum, your facility should have identified RAGAGEPs for each of the following types of equipment:
- Pressure vessels and storage tanks
- Piping systems (including piping components such as valves)
- Relief and vent systems and devices
- Emergency shutdown systems
- Controls (including monitoring devices and sensors, alarms, and interlocks)
- Pumps
- Equipment deficiencies: Your Mechanical Integrity policy document should explicitly mention equipment deficiencies, including the definition of what counts as an equipment deficiency, as well as what steps should be taken when an equipment deficiency is discovered. This should include steps to shut down the process and/or ensure the process can run safely until maintenance is performed.
- Quality assurance: Your Mechanical Integrity policy document should also have a section on quality assurance. This section should include a discussion of the following topics:
- Process equipment: Quality assurance for process equipment should include:
- Fabrication: State how the facility will make sure that process equipment as it is fabricated is suitable for the process. This may involve reviews during the management of change (MoC) process, complying with identified RAGAGEPs and your organization's engineering standards and/or reviews during the PSSR process.
- Installation: State how the facility will make sure that equipment is installed properly, consistent with the manufacturer’s instructions and consistent with design specifications.
- Maintenance equipment: Quality assurance for maintenance equipment should include:
- Materials: State if any special maintenance materials are required, such as non-sparking tools for use in electrically classified (hazardous) areas.
- Spare parts: State the logic for identifying which spare parts will be kept on hand, as well as if any special spare parts are required. For example, special gaskets may be needed for handling solvents.
- Process equipment: Quality assurance for process equipment should include:
Management of Change
MoC programs do not have to be highly sophisticated, but the program must include specific items. Make sure that your MoC form or tool contains fields to address each one of the following “magic words.”
- Technical basis for the proposed change
- Impact of change on safety and health
- Modifications to operating procedures
- Necessary time period for the change
- Authorization requirements
Incident Investigation
Regardless of whether your facility is using a paper form or an electronic platform, the initial incident report and subsequent incident investigation should capture the following elements.
- Initial incident report
- Date of incident
- Description of the incident
- Incident investigation: The incident investigation report should include the following “magic word” sections:
- Date investigation began: Make sure the investigation report has a line item to record the date that the investigation started. Best practice is to record when the investigation was completed as well.
- Factors that contributed to the incident: Remember to never blame the employee. This is best not done only as a checklist but rather to use a root cause analysis to identify contributing factors.
- Recommendations: The recommendations should be generated to address both the contributing factors and the root cause.
- Resolutions and corrective actions: Once recommendations have been generated, the facility will need to track them to completion. More importantly, it is not sufficient to mark the action as complete – supporting evidence needs to be included. This should include the name of the employee(s) who took action, evidence of completion, and the date of completion.
- Reviews with employees/contractors: This requirement often gets overlooked. The facility needs to document that the incident investigation was reviewed with employees and contractors who work in that area or with that process. Best practice is to document not only that the information was communicated, but also who received the information and how.
Emergency Response
Emergency response is required by a number of different entities, which all have slightly different requirements and slightly different names for the emergency response documentation. OSHA calls it the EAP, while the EPA calls it the Emergency Response Plan (ERP). The federal government agrees that the name of the emergency response document does not matter, so long as the document contains all the required information. Below is a summary of that required documentation, broken down by regulation.
- OSHA EAP minimum elements: The OSHA PSM standard (29 CFR 1910.119) cross-references to the OSHA emergency action plan standard (29 CFR 1910.38). If your facility is subject to the PSM regulations, then these are the “magic words” that should be in your plan. You can always add more to your document, but this is the minimum.
- Procedures for reporting a fire or other emergency: Step-by-step instructions for employees to report an emergency within your facility. This may include pulling a fire alarm, using a cell phone, and/or calling a guardhouse.
- Procedures for emergency evacuation: Step-by-step instructions for evacuation, including the nearest exit, identification of the muster point(s), and possible secondary muster point(s).
- Procedures to be followed by employees who remain to operate critical plant operations before they evacuate: Even if your facility decides that no one will remain behind, these “magic words” should still be in your plan, followed by a statement that no employees are to stay behind.
- Procedures to account for all employees after evacuation: The plan should outline who is responsible for taking attendance, how attendance will be taken, and how to account for any contractors or other non-routine personnel onsite.
- Procedures to be followed by employees performing rescue or medical duties: This may include the types of rescue (i.e., confined space) or medical duties (i.e., first aid) that employees are trained to perform, if your facility decides to train personnel. Alternatively, your facility may decide that employees are not required to perform rescue or medical duties. In this case, the “magic words” still need to be in your plan, along with a sentence that the facility does not require employees to perform rescue or medical duties.
- The name or job title of the people who may be contacted for more information about the plan: This is one of the most often omitted portions of the EAP. Make sure you have these “magic words” in your EAP.
- EPA ERP minimum elements: The EPA RMP standard (40 CFR 68) requires three items within the ERP. If your facility is subject to the RMP regulations, then these are the “magic words” that should be in your plan. Note that the RMP regulation also allows you to keep the information within a written plan that complies with other federal contingency plan regulations, such as the National Response Team's Integrated Contingency Plan Guidance (“One Plan”).
- Procedures for informing the public and the appropriate federal, state, and local emergency response agencies about accidental releases: This should include a list of agencies and their contact information. You can also identify who is responsible for contacting these agencies.
- Documentation of proper first-aid and emergency medical treatment: This is similar to the OSHA requirement above but actually requires that the facility have first aid equipment available in case of an emergency.
- Procedures and measures for emergency response after an accidental release: This should be a step-by-step guide for how to respond to an accidental release. The facility may choose to clean up incidental spills themselves. If so, then these policies and practices should be documented in the ERP. Likewise, if the facility chooses to rely on an outside entity for emergency response, this should be outlined in the ERP.
- Fire prevention plan minimum elements: If your facility has a process that uses a flammable liquid, then your facility may also be subject to OSHA’s fire prevention plan (FPP) requirements in 29 CFR 1910.39. This has additional “magic words” that must be included. Your facility can choose to have a combined EAP and FPP or make them two separate documents.
- A list of all major fire hazards: For a large facility, this list could be extensive. The list should include each fire hazard as well as the location of the hazard within the facility.
- Proper handling and storage procedures for hazardous materials: This should be the standard procedures that employees would use to handle and store hazardous materials and should be as detailed as possible.
- Potential ignition sources and their control: Best practice is to add columns to the list of major fire hazards above, identifying nearby potential ignition sources, and how the facility prevents the ignition sources from being a cause for concern.
- Type of fire protection equipment necessary to control each major hazard: Best practice is to add another column to the list of major fire hazards above, with a column to identify the fire protection equipment that protects each hazard.
- Procedures to control accumulations of flammable and combustible waste materials: This should be a list of management practices that the facility uses to limit accumulations of flammable waste materials.
- Procedures for regular maintenance of safeguards installed on heat-producing equipment to prevent the accidental ignition of combustible materials: The facility can tie this requirement into the mechanical integrity program, so long as the MI program identifies the types of maintenance for this equipment. Note that this should include heat tracing, boilers, and heat exchangers.
- The name or job title of employees responsible for maintaining equipment to prevent or control sources of ignition or fires: This is one of the often-missed required elements. Note that this is usually the maintenance manager but may include other personnel onsite as well.
- The name or job title of employees responsible for the control of fuel source hazards: This is generally the person who is responsible for maintaining the FPP.
Business Benefits
When you incorporate these “magic words” into your PSM or RMP program documentation, you’ll gain several benefits, including:
- Regulatory compliance: If you are ever audited by a regulatory body, you should be easily able to demonstrate compliance with the applicable regulation.
- Easy compliance audits: When it’s time to conduct a regulatory-required compliance audit, your auditor will be easily able to find the required elements and mark them as compliant.
- Seamless transitions: When you have new personnel take over the PSM or RMP Coordinator role, the new person will be able to quickly take stock of the program and verify compliance.
Summary
“Magic words” is a term I use to refer to those regulatory-required elements that should be included in various aspects of your facility’s PSM and/or RMP program but are often overlooked or missing. Including these “magic words” is an easy way to help make sure your facility is in compliance with the regulations. You can use the terms highlighted in bold in this paper as a means to check your facility.
Need Help?
Jensen Hughes is here for you. We have a team of process safety professionals with expertise in implementing PSM and RMP programs, evaluating code compliance, and conducting PHAs. We’ve built RMP and PSM programs from the ground up, assisted with RMP filings, conducted hundreds of PHAs and root cause investigations, and have deep experience with EPA and OSHA requirements. Contact us today to see how we can augment your team.
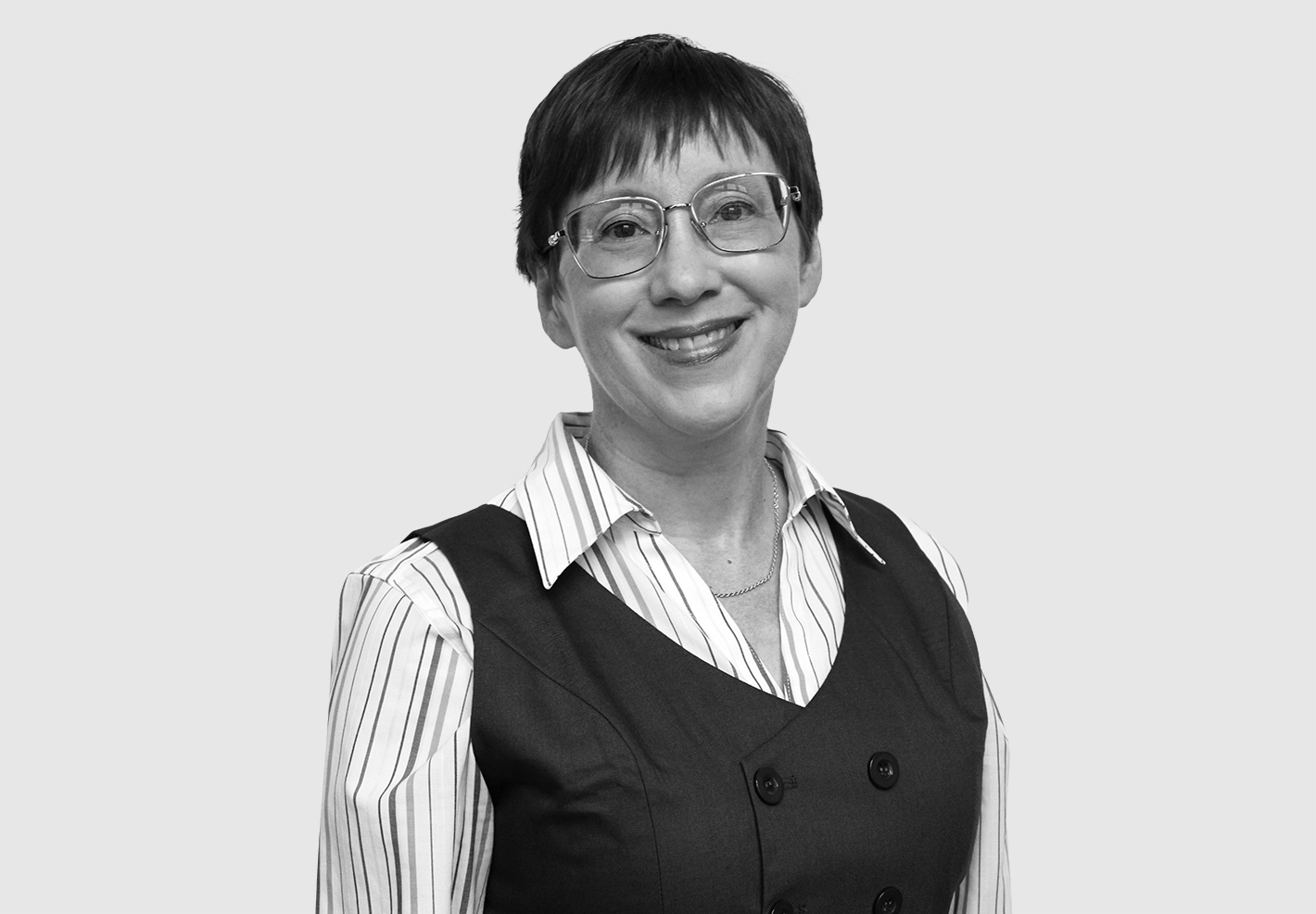
About the author
Sign up to receive the latest updates, news and insights from Jensen Hughes!
Connect With UsGet In Touch
ContactMore blog posts from Jensen Hughes
CE Marking vs. UL 9540: Understanding Global Safety and Compliance for BESS
Apr 29, 2025
CE marking alone isn’t enough for BESS safety compliance in North America. Learn the key differences between CE and UL 9540 certifications—and why both may be needed for global deployment under evolving regulations.
Countdown to Compliance: What the CMS Sprinkler Requirement Means for Your High-Rise Healthcare Facility
Apr 25, 2025
Get ahead of the CMS sprinkler compliance deadline. High-rise healthcare facilities must meet NFPA Life Safety Code by July 5, 2028—no exceptions. Start your facility assessment and compliance plan with Jensen Hughes today.
Fire-Resistive Duct Assemblies - A Comparison of International Test Methods and Applications for U.S. Code Requirements
Apr 23, 2025
Explore how to assess international duct fire-resistance tests for U.S. code compliance using IBC Section 104.11 and ASTM standards. Download the whitepaper.