Why Life Safety Code® Assessments (LSCA) Are Critical in Health Care Facilities
Paul Dzurinda
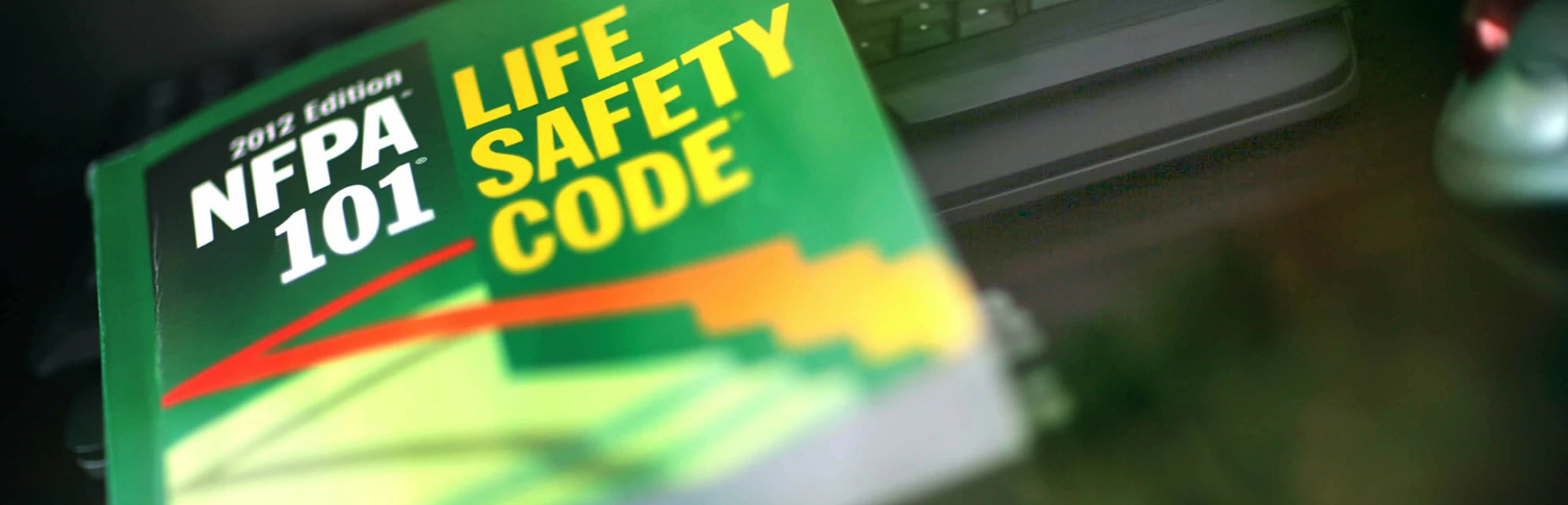
Apr 23, 2025
During fire emergencies in health care facilities such as hospitals, nursing homes and surgery centers, staff rely on the “defend-in-place” approach to protect patients. Using this approach, staff can relocate incapacitated patients horizontally to an adjacent smoke compartment where life-saving medical treatment can continue. Building evacuation is relied upon as a last resort, depending on the magnitude and progression of the fire.
For the “defend-in-place” approach to work, the federal Centers for Medicare & Medicaid Services, and accrediting organizations such as The Joint Commission, Det Norske Veritas and others, require compliance with NFPA 101, Life Safety Code® (2012).
NFPA 101 (2012) requires health care facilities to have specific fire protection features in place. Examples include protected structural elements, smoke barriers/compartmentation, fire alarm systems and fire suppression systems. Since fires are unpredictable, fire protection features must always be in a state of complete readiness to protect occupants; the breakdown of any one feature can lead to catastrophic outcomes.
To ensure that NFPA 101 requirements are met, and that the fire protection features supporting the “defend-in-place” approach will be successful if called upon during fire emergencies, it is critical that Life Safety Code Assessments (LSCA) are conducted on a frequent basis.
The Health Care Life Safety Code® Assessment (LSCA)
The most effective way to measure compliance with the Life Safety Code is by conducting Life Safety Code Assessments (LSCA). The LSCA is a comprehensive, systematic approach to assessing the physical condition of the building, documenting items not in compliance with Life Safety Code requirements and developing plans to manage noncompliance.
Who Can Conduct the LSCA
It is imperative that an LSCA is conducted by a team that has in-depth knowledge and understanding of applying Life Safety Code provisions (including applicable referenced standards) to health care facilities. Not only are there many nuances involved with applying the Life Safety Code, but there are several authorities having jurisdiction within the health care realm, and at times, each might have their own interpretations of Life Safety Code requirements. In this regard, misapplication of the code may lead to fire safety issues being neglected during the LSCA. Conversely, items that are not true deficiencies might be identified, thus leading to unnecessary expenditures.
To ensure that the Life Safety Code is accurately applied, many health care organizations partner with a third-party vendor to conduct an LSCA. Not only do third-party vendors bring along extensive knowledge and experience, but they also provide the distinct advantage of being able to view the organization’s level of compliance in a neutral, unbiased manner.
Conducting the LSCA/Identifying Areas of Noncompliance
Using the Life Safety Drawings as a roadmap, the facility is assessed using a systematic “top-down” approach. The assessment starts at the roof level and progresses downwards to the lowest level of the facility, with each area/room being assessed.
To be efficient, it is recommended that the drawings be downloaded to a mobile device or tablet for use during the LSCA. Using this method, non-compliant items are documented in real-time with the following information:
- The exact location (floor, area, room) of each deficiency. Pictures should be included, if needed, to provide clarity.
- Specific details of each deficiency type, including NFPA codes or standards driving the requirement. Grouping deficiency types in a meaningful way such as the following is helpful: Buildings, Rated Barriers, Opening Protectives, Egress, Extinguishment, Fire Alarm, Medical Gas, Electrical and Operational.
- Recommended actions for correcting each deficiency. Oftentimes, there are multiple solutions to consider.
Managing Noncompliance
During the initial LSCA, a multitude of items needing attention are typically identified, and as such, managing noncompliance can seem like a daunting task. However, by having the results of the LSCA documented in an organized and concise manner, managing the LSCA becomes much more efficient. For example, the documentation method should include:
- A means for prioritizing deficiencies for correction.
- A means for documenting alternative life safety measure assessments/implementation.
- A means for “closing the loop” on deficiencies. Tracking progress via the use of dashboards is beneficial when reporting out to upper management.
Continual Assessment
Performing the LSCA is not a one-time event. Health care facilities are constantly in a state of flux, and therefore, it is important that the building be assessed on a continual basis. During each assessment, quality control measures are used to verify that previously identified deficiencies have been properly corrected. In addition, new deficiencies that may have arisen since the last assessment are identified. Establishing a partnership with a third-party vendor to perform an assessment cycle starting with a full LSCA, followed by continual “spot checks,” has proven to be extremely valuable.
Our Approach to LSCA Support
At Jensen Hughes, we specialize in conducting LSCA for a wide range of health care facilities – from large, multi-building hospital campuses to smaller ambulatory surgical centers and medical office buildings.
We use our online platform, ProtectAdvisrTM, to organize and document assessment findings. This allows organizations to easily search for deficiency types or locations and assign follow-up actions. ProtectAdvisr also helps teams track their LSCA progress through customizable dashboards. Each report includes deficiencies, and current Life Safety Drawings are produced – an essential item needed to effectively manage compliance.
Look for future posts in which we discuss each LSCA deficiency category in more detail. Using data from ProtectAdvisr, we will illustrate common deficiencies discovered across the nation.
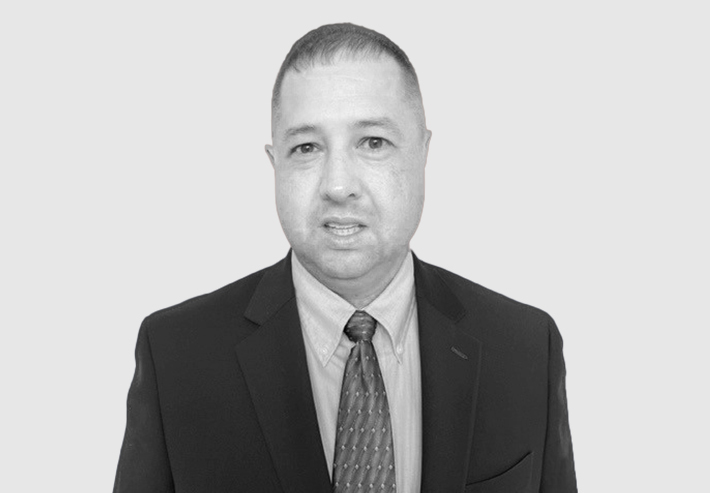
About the author
Sign up to receive the latest updates, news and insights from Jensen Hughes!
Connect With UsGet In Touch
ContactMore blog posts from Jensen Hughes
From Buzzword to Bottom Line: Bridging the AI Implementation Divide
May 12, 2025
Many AI projects fail chasing big transformations. Real impact starts with small wins—solving everyday problems for faster ROI and lasting adoption.
Fire Protection in Aircraft Hangars: Adapting to Changes in NFPA 409
May 7, 2025
Discover how the innovative, foam-free fire protection solutions for Belgium’s F-35 aircraft hangars were developed to meet strict safety standards
CE Marking vs. UL 9540: Understanding Global Safety and Compliance for BESS
Apr 29, 2025
CE marking alone isn’t enough for BESS safety compliance in North America. Learn the key differences between CE and UL 9540 certifications—and why both may be needed for global deployment under evolving regulations.